单晶金刚石刀具
在超精密加工中,保证加工表面质量的主要因素除了高精度的机床、超稳定的加工环境外,高质量的刀具也是很重要的一个方面。单晶金刚石具有硬度高、耐磨性好、强度高、导热性好、与有色金属摩擦系数低、抗黏结性好以及优良的抗腐蚀性和化学稳定性,可以磨出极其锋利的刀刃,被认为是最理想的超精密切削用刀具材料,在机械加工领域尤其是超精密加工领域有着重要地位并得到广泛应用。
二十世纪七十年代后期,在激光核融合技术的研究中,需要大量加工高精度软质金属反射镜,要求软质金属表面粗糙度和形状精度达到超精密水平。如采用传统的研磨、抛光加工方法,不仅加工时间长、费用高、操作难度大,而且不易达到要求的精度。因此,亟需开发新的加工方法。在现实需求的推动下,单晶金刚石超精密切削技术得以迅速发展。由于单晶金刚石本身的物理特性,切削时不易黏刀及产生积屑瘤,加工表面质量好,加工有色金属时,表面粗糙度可达Rz0.1~0.05μm。单晶金刚石刀具还能有效地加工非铁金属材料和光学材料,如金、银、铜、铝等有色金属及蓝宝石、硒化锌、硫化锌、硅、Ge、氟化钙、氟化钡、光学玻璃、陶瓷晶体等光学材料。
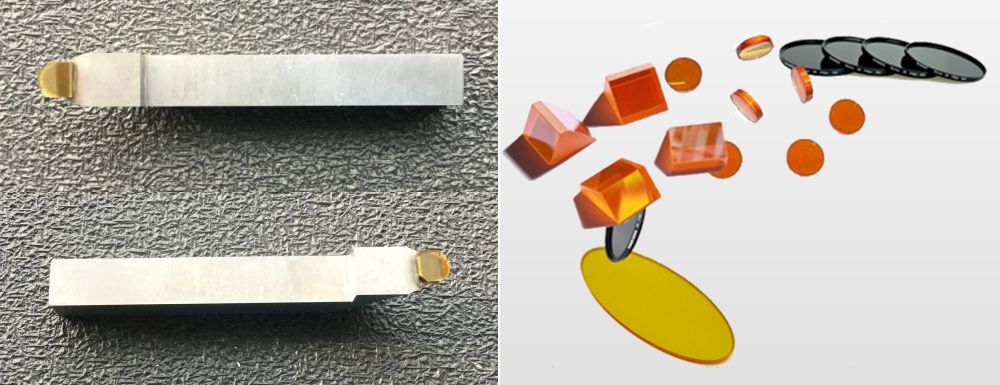
超精密加工中,单晶金刚石刀具的两个基本精度是刀刃轮廓精度和刃口的钝圆半径。要求加工非球面透镜用的圆弧刀具刃口的圆度为0.05μm以下,加工多面体反射镜用的刀刃直线度为0.02μm;刀具刃口的钝圆半径(ρ值)表示了刀具刃口的锋利程度,为了适应各种加工要求,刀刃刃口半径范围从20nm~1μm。
金刚石晶体属于平面立方晶系,由于每个晶面上原子排列形式和原子密度的不同以及晶面之间距离的不同,造成天然金刚石晶体的各向异性,因此金刚石不仅各晶面表现的物理机械性能不同、其制造难易程度和使用寿命都不相同,各晶面的微观破损强度也有明显差别。金刚石晶体的微观强度可用Hertz试验法来测定,由于金刚石是典型的脆性材料,其强度数值一般偏差较大,主要依赖于应力分布的形态和分布范围,因此适合用概率论来分析。当作用应力相同时,(110)晶面的破损概率最大,(111)晶面次之,(100)晶面产生破损的概率最小。即在外力作用下,(110)晶面最易破损,(111)晶面次之,(100)最不易破损。尽管(110)晶面的磨削率高于(100)晶面,但实验结果表明,(100)晶面较其它晶面具有更高的抗应力、腐蚀和热退化能力。结合微观强度综合考虑,用(100)面做刀具的前后刀面,容易刃磨出高质量的刀具刃口,不易产生微观崩刃。
通常应根据刀具的要求来进行单晶金刚石刀具的晶面选择。一般来说,如果要求金刚石刀具获得最高的强度,应选用(100)晶面作为刀具的前、后刀面;如果要求金刚石刀具抗机械磨损,则选用(110)晶面作为刀具的前、后刀面;如果要求金刚石刀具抗化学磨损,则宜采用(110)晶面作刀具的前刀面,(100)晶面作后刀面,或者前、后刀面都采用(100)晶面。这些要求都需要借助晶体定向技术来实现。
目前,晶体定向主要有三种方法:人工目测晶体定向、激光晶体定向和X射线晶体定向。
人工目测晶体定向:该方法是根据天然晶体外部几何形状、表面生长、腐蚀特征及各晶面之间的几何角度关系,凭借操作者长期的工作经验,通过观察和试验所做的粗略晶体定向。该方法简单、易行、不需要借助设备,但定向结果准确性差,对操作者经验要求高,且对于经过加工、失去了天然单晶晶体特征的刀具就无法再进行人工目测定向。
激光晶体定向:激光晶体定向是用相干性较好的激光照射到金刚石晶体表面上,在不同结晶方向上表面存在的在生长过程中形成的形状规则的晶面晶纹和微观凹坑被反射到屏幕上形成特征衍射光图像。但实际上因受到外界干扰因素,自然形成的规则晶面晶纹和微观凹坑往往不明显或根本无法观察到。因此这种晶体在定向之前,要经过适当的人工腐蚀,以形成特征形貌。
X射线晶体定向:由于X射线的波长接近晶体的晶格常数,当X射线透过晶体或从晶体表面反射回来时,会发生衍射。利用这个原理已开发有专用的X射线晶体定向仪。这种晶体定向方法精度高,但是因X射线对人体有一定的危害,在使用时需注重对操作人员的保护。
金刚石刀具的晶向选择:金刚石各向异性,因此不但各晶面的硬度、耐磨性不同,就是同一晶面不同方向的耐磨性也不同。如果晶向选择不当,即使晶面选择正确,刃磨效率也会大大降低。同时由于金刚石晶体的抗压强度比抗拉强度大5~7倍,所以在刃磨过程中要选择晶面的易磨方向,同时刃口要迎着刃磨砂轮线速度的正方向(即采取逆磨),以保证刃磨效率并减小刃口的微观解理程度。
金刚石刀具的磨、破损:金刚石刀具的磨损机理比较复杂,可分为宏观磨损和微观磨损,前者以机械磨损为主,后者以热化学磨损为主。常见的金刚石刀具磨破损形态为前刀面磨损、后刀面磨损和刃口崩裂。在单晶金刚石刀具刃磨过程中,需要其磨损以刃磨出满足要求的刀具,但若产生了不需要的磨损就可能损伤已经刃磨好的前、后刀面。而刃口崩裂(即崩刃)是在刃口上的应力超过金刚石刀具的局部承受能力时发生的,一般是由金刚石晶体沿(111)晶面的微观解理破损造成的。在超精密加工中,金刚石刀具的切削刃钝圆半径比较小,其本身又属于硬脆材料,同时由于其各向异性且(111)面易发生解理,随着振动和砂轮砂粒对刀具刃口的冲击作用,故常常会伴随产生崩刃现象。
由于刀具的要求,或金刚石形状所决定,有时候需要将金刚石原石分割。金刚石具有平行完全解理,金刚石中的碳原子与碳原子之间是以较大力量的共价键结合在一起的。但是在金刚石结构中的某些特定方向,如平行八面体面方向施加一定的力后,金刚石非常容易破裂,主要是因为金刚石晶体中连接此面的键相对较少。因此选择金刚石的解理面进行分割原石,劈开的方法如图1 所示。在需要劈开的金刚石上开出一条称为切缝的槽或刻痕。劈开的技巧在于知道从哪里开缝以及要切多深。切缝要想磨出一把高质量单晶金刚石刀具,必须掌握单晶金刚石的晶体定向技术。这主要是由于单晶金刚石的各向异性的特点决定的,金刚石的各个方向上的硬度差别很大。要选择合适的晶面和晶向作为刀具的前刀面、后刀面,即刀刃,使其耐磨性和加工性能达到最好。金刚石晶体各界面在好磨方向上, 晶面的磨削率最低, 晶面次之, 晶面磨削率最高。由于晶面硬度太高,研磨加工困难,而且微观强度不高,易解理,很难磨出锋利刃口。晶面在好磨方向上磨削率比晶面高近一倍, 但从金刚石不同晶面产生破损的机率来适用各种型号的电机进行综合保护,对于不同的电机只需调整相应阀值即可。